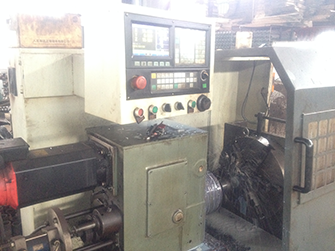
托輥焊接—組裝—檢測流水線
該線與上游管加工流水線直接相連,我們設(shè)計專用的工裝卡具,采用直接組裝、定位基準(zhǔn)的方式,依次送入軸、壓入軸承,以
托輥軸兩端外徑為基準(zhǔn),直接與管體外徑定位焊接,保證了軸的
精度和工裝卡具的精度,甩掉了通常托輥裝配中采用的多個零件
次序組裝、逐級定位的方式所產(chǎn)生的累積誤差,確保了最終托
輥產(chǎn)品的精度要求。在焊接后,再注入油脂、壓入密封、裝配
卡環(huán),以上裝配過程全部經(jīng)過流水線完成生產(chǎn),并通過檢測流
水線完成托輥的徑向跳動與旋轉(zhuǎn)阻力的檢測。經(jīng)檢驗(yàn)合格的
托輥安裝精度高,內(nèi)應(yīng)力小,托輥的旋轉(zhuǎn)阻力小,質(zhì)量穩(wěn)定,
有效避免了手工操作產(chǎn)生的誤差和不穩(wěn)定性,托輥使用壽命大大提高。

軸承座加工流水線
沖壓完成的軸承座,需經(jīng)加工機(jī)精車以便提高其外緣精度,滿足與管內(nèi)止配合的公差要求,按照裝配工藝此處為過盈配合,定位準(zhǔn)確,可以有效防止其他廠家常用的間隙配合導(dǎo)致的定位不準(zhǔn)問題。精車之后的軸承座,與送入的軸承自動壓成一體作為組件輸送給托輥焊接組裝線。寶科機(jī)械通過準(zhǔn)確定位,軸承與軸承座的預(yù)裝,高精度焊接有效地保證了托輥的同軸度要求,大幅減小了裝配中產(chǎn)生的內(nèi)應(yīng)力和焊接熱變形。
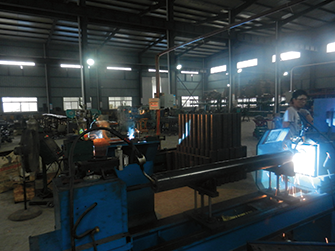
噴漆—干燥流水線
檢測合格的托輥經(jīng)除灰、除油等表面處理后,進(jìn)入由懸掛鏈?zhǔn)捷斎霗C(jī),靜電發(fā)生裝置,噴漆通道。干燥設(shè)備構(gòu)成的靜電噴漆干燥流水線,完成表面涂裝。寶科機(jī)械托輥使用的涂料中添加有防銹成分,干燥后所形成的漆膜堅硬。耐水,耐油,耐酸,附著力強(qiáng),美觀精致,適用各種工況。
檢查通過的鋼管被送入自動管加工機(jī)。管材切斷后,對鏜雙側(cè)止口,高壓氣體清掃管內(nèi)鐵屑和雜質(zhì)。
對于輥皮的加工,無論是輥皮的內(nèi)外取面,還是軸承座組件對應(yīng)的鑲合部位,都是在高精度的工藝保證狀況下進(jìn)行的,采用一點(diǎn)定位,多點(diǎn)加工的方式一次完成。

軸承座;沖壓流水線
冷軋帶鋼由自動侍服系統(tǒng)送入流水線,使用6臺:沖壓機(jī)連續(xù):沖壓成形。各臺:沖壓機(jī)通過搬動機(jī)械手連接在一起,保證了高效穩(wěn)定的生產(chǎn)能力。寶科機(jī)械全部采用進(jìn)品;沖壓模具和進(jìn)品冷軋帶鋼,使軸承座的內(nèi)徑公差保持在0.019mm之內(nèi),遠(yuǎn)低于國家標(biāo)準(zhǔn)規(guī)定的O.04mm。
通過限定;沖壓速度、;沖壓通力、油脂使用量等指標(biāo)來最大限度地控制壓延過程中板材厚度的減小,保證了軸承座的強(qiáng)度要求。針對濕熱工況,我們對:沖壓完成的軸承座還要進(jìn)行磷化處理以增強(qiáng)防腐能力.
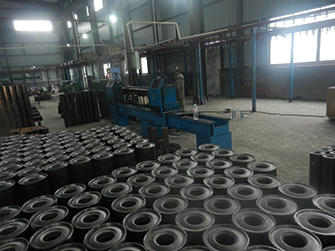
軸加工流水線
寶科機(jī)械采用表面精度較高的冷拉圓鋼作為軸材,軸材按設(shè)定長度切斷,
進(jìn)給至卡裝位,依次進(jìn)行打中心孔,車卡環(huán)槽。倒角和銑扁四道工序,整個
過程全部在同一工位自動完成,不會產(chǎn)生因多次卡裝造成的累計誤差過大的
現(xiàn)象,設(shè)備采用一點(diǎn)定位多點(diǎn)加工的方式進(jìn)行生產(chǎn),避免了因多次夾裝、定
位產(chǎn)生的累計誤差過大的現(xiàn)象,同軸度、圓柱度均好于其他同業(yè)。
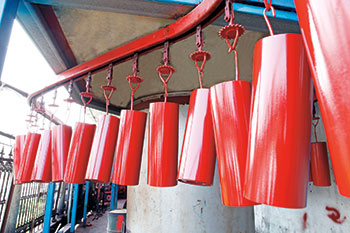